AyMINE – Technischer Bericht (Englisch)
Module
Aufgaben-, Projekt- und Qualitätsmanagement
Aufgaben-, Projekt- und Qualitätsmanagement
Systemrechte für das Task-Management-Modul
Task Management Modul Verwaltung
Benachrichtigungen und Nachrichten
Benachrichtigungen an sich selbst
FMEA – Auftretenswahrscheinlichkeit
FMEA – Wahrscheinlichkeit der Entdeckung
Fehleranalyse für eine einzelne Eigenschaft eines Bauteils oder Prozesses
Methodik und Qualitätsmanagementsystem
Probleme, Tickets und ihre Verwaltung
8D report – Systemunterstützung
Kundenservice Antwortgenerierung
Qualifikation, Fähigkeit / Geschicklichkeit
GDPR und Verzeichnis der Qualifikationen
Qualifikation des Benutzers oder Kontakt
Rechte zur Verwaltung der Qualifikationen von Nutzern
Kontakte, Verzeichnisse
System-Berechtigungen und CRM-Modul-Einstellungen
Adressbuch von Personen und Firmen
Massenversand von Nachrichten in Übereinstimmung mit der GDPR
Melden Sie sich ab und stellen Sie Einstellungen ein
für Massenmails
Wie man die Daten einer Person richtig vergisst
Web-Management und Automatisierung
Web-Management und Automatisierung
Benutzerdokumentation für AyMINE
Empfangen einer Nachricht über das Web
Grundlegende Service-Einstellungen
Zugriff auf eine Website speichern
HR-Modul
Abteilung verwalten / division data
Personalistics – Benutzerberechtigungen
Registrierung von Arbeitsuchenden
Sicherheit der Personalverwaltung
Ein Überblick über Ihr eigenes Mitarbeiter
Synchronisierende Mitarbeiter und Benutzer des Systems
Produkte, Vermögenswerte, Kauf und Verkauf
Produkte, Vermögenswerte, Kauf und Verkauf
Angebot und Preis Zugriffsrecht
Erhaltener Auftrag für Waren oder Dienstleistungen
Produkteigenschaft oder Produktelement
Finanzmanagement
Metriken und Messungen
Technische Module
Sabre-Modul
Konnektor zwischen AyMINE und Enterprise Architect
Datenbanklink zur Enterprise Architect Datenbank
Konnektor zwischen AyMINE und Enterprise Architect
Systemmodule
Framework – Systembasis
Richtlinie zur Aufbewahrung von Passwörtern
Überblick über Module und Datentypen
AyMINE — Anwendung für Windows
Drag & Drop zwischen den Datensätzen
Gesten und Tastenkombinationen
Konfigurieren Sie, wie Ihr System aussieht und funktioniert
Mehr darüber, wie das System funktioniert
Private Notizen und Tags für Objekte
Systemverwaltung
Beziehungen zwischen den Datensätzen
Formatierte Texte in der Anwendung
Gateway-Einstellungen für externe -Nachrichten
Regeln für externe Nachrichten
Sichere Geschäftskommunikation
FMEA-Analyseprozess
Der FMEA-Analyseprozess besteht aus 7 Schritten
FMEA-Methodik in AyMINE
AyMINE hat eine vorbereitete Methodik für den FMEA-Prozess (natürlich können Sie diese anpassen oder Ihre eigene Methodik erstellen).
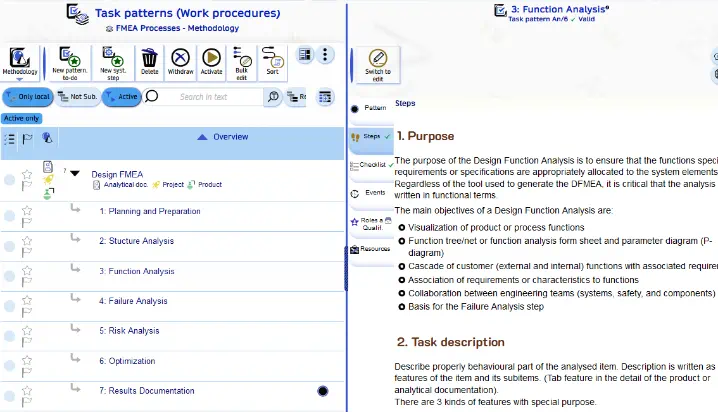
Es genügt, eine Reihe von Aufgaben nach den Vorlagen in der Methodik zu generieren.
Überblick über die FMEA-Schritte
Die Abschnitte beschreiben nicht den gesamten Prozess, sondern seine Implementierung innerhalb von AyMINE. Für ein vollständigeres Verständnis von FMEA empfehlen wir unsere Schulung. Details sind auch direkt in den Prozessdetails innerhalb der FMEA beschrieben. Ziel dieser Seite ist es, einen globalen Überblick über den Prozess zu geben, der aus den einzelnen Aufgaben möglicherweise nicht ausreichend ersichtlich ist.
Schritt 1 - Planung und Vorbereitung
Die Vorbereitung der FMEA wird durch den standardisierten FMEA-Prozess geleitet. Der Prozess kann vom Projektleiter oder dem für das Produkt verantwortlichen Eigentümer initiiert werden. Er sollte mit dem analysierten Produkt oder Prozess verknüpft sein. Die Verknüpfung ist sowohl mit einem bereits in der Produktdatenbank erfassten Produkt als auch mit Analyseelementen, also z. B. einem Produktionsprozess, möglich.
Ein zentraler Bestandteil des ersten Schritts ist die Definition des Teams, das die FMEA-Analyse durchführt. Der Leiter nominiert die Teammitglieder für die Analyseaufgabe – nicht für die Vorbereitungsaufgabe, die in seiner Verantwortung liegt.
Der Zeitplan für die nächsten Schritte hängt von der Verfügbarkeit und Größe des Teams ab:
- Verantwortung für die Überprüfung und ggf. Ergänzung der Analyse des analysierten Objekts. Die verantwortliche Person erhält die Aufgabe FMEA - Schritt 2.
- Verantwortung für die Vorbereitung der Funktionsanalyse - FMEA - Schritt 3.
- Einladung von Experten zu einem Treffen zur Analyse von Fehlern und Risiken. Diese sollten sich im Voraus mit der Analyse vertraut machen können, daher sollte zwischen den Schritten 2 und 3 und dem Beginn von Schritt 4 genügend Zeit liegen (die Dauer hängt davon ab, ob unabhängige Experten einbezogen werden, die das Thema nicht kennen).
Ein weiterer wichtiger Bestandteil ist die Planung analytischer Sitzungen zur Durchführung der Schritte 4 und 6.
Eine qualitativ hochwertige Planung und Vorbereitung mag teilweise selbstverständlich erscheinen, teilweise überflüssig. Doch gerade eine gute Vorbereitung entscheidet darüber, ob die Analyse effektiv ist.
- Es ist notwendig, den Umfang der Analyse klar zu definieren. Genauer gesagt, wo genau die Grenzen des analysierten Objekts (Prozess, Produkt) liegen.
- Es muss geprüft werden, wer das Thema wirklich versteht, und ein kompetentes Team zusammengestellt werden.
- Die Vorbereitung, insbesondere die Vorbereitung der Unterlagen, sowie alle weiteren Schritte müssen geplant werden.
Schritt 2 - Strukturanalyse
Das Ergebnis ist die Struktur des Objekts entweder in Form von Komponenten (für ein Produkt) oder Prozessschritten und verwendeten Geräten (für einen Prozess).
Wenn für die Strukturanalyse eine Produktanalyse verwendet wird, können die Ergebnisse der Strukturanalyse mithilfe von Enterprise Architect visualisiert werden. (Dies erfordert eine Verbindung über den eacon-Connector zum EA-Modell.)
Bei der Verwendung einer dokumentierten Bauteilbasis ist es möglich, an bereits vorhandene frühere FMEA-Analysen anzuknüpfen. Es ist daher ratsam, nach Möglichkeit bereits erfasste Teile zu verwenden und keine Duplikate innerhalb der Strukturanalyse zu erstellen.
Schritt 3 - Funktionsanalyse
Das Ergebnis sind Beschreibungen der Eigenschaften, Betriebsmodi und Zustände der einzelnen Einheiten im Detail. Auf Bauteilebene sollten die für FMEA relevanten Eigenschaften der Bauteile beschrieben werden. Die Beschreibungen sind direkt mit den Elementen verknüpft, sodass die Funktionsanalyse logisch erst nach der Strukturanalyse durchgeführt werden kann.
Das grundlegende Kontrollinstrument der Funktionsanalyse ist die Erfüllung der funktionalen Spezifikation des Produkts bzw. Prozesses anhand von Eigenschaften (ein allgemeiner Begriff, der Folgendes umfasst):
- Allgemeine Eigenschaft
- Funktionalität
- Betriebsmodus
Wenn eine wiederholte FMEA-Analyse eines Teils für einen anderen Zweck durchgeführt wird, können die Dokumentationen aus der vorherigen Analyse genutzt oder eine neue Analyse für dasselbe Element erstellt werden. Daher kann für jede Eigenschaft angegeben werden, in welche Analyse sie aufgenommen wurde. (Wenn dies nicht angegeben ist, ist sie in allen enthalten.)
Schritt 4 - Fehleranalyse
Mögliche Fehler werden für einzelne Eigenschaften erfasst. Für jede Eigenschaft können Fehler in einem Schritt eingetragen werden, aber es ist besser, sie einzeln in Fehlerfälle aufzuteilen (Registerkarte im Detailbereich).
Die dokumentierten Fehlerfälle werden Teil der Dokumentation der jeweiligen Eigenschaft bzw. des Bauteils (oder Prozessschritts). Mit ihnen wird in Schritt 5 weitergearbeitet.
Jedes Bauteil und jede Eigenschaft wird separat erfasst, daher ist es problemlos möglich, die FMEA-Analyse in mehrere Gruppen zu unterteilen, wenn dies aufgrund unterschiedlicher Eigenschaften sinnvoll ist.
Schritt 5 - Risikoanalyse
Die Risikoanalyse baut auf der Fehleranalyse auf – sie ergänzt die Informationen zu den in Schritt 4 der FMEA erfassten Fehlerfällen. Grundsätzlich sollten in der FMEA keine neuen Zeilen hinzugefügt werden – diese entsprechen den möglichen Fehlern, aber die bereits identifizierten werden weiter untersucht.
Schritt 6 - Optimierung
Wie Schritt 5 basiert auch Schritt 6 auf der Vorbereitung aus den Schritten 2 und 3. Für jeden Fehler und jede Risikoanalyse berechnet das System die Priorität der Maßnahmen zur Risikominimierung. (Das System berechnet auch den älteren RPN-Wert, da viele Teams immer noch an diesen Index gewöhnt sind.)
Ein wichtiger Bestandteil der Optimierung ist die Entwicklung von Änderungen, die die Eintrittswahrscheinlichkeit verringern. Für jeden Fehler können sowohl bestehende Maßnahmen zur Minimierung als auch neu vorgeschlagene Maßnahmen unterschieden werden.
Im Rahmen der Analyse werden die neuen Maßnahmen dokumentiert, und die erwarteten Werte werden erfasst – das Ergebnis der Analyse zeigt somit nicht nur den aktuellen Zustand, sondern auch den Zustand nach der Umsetzung aller Maßnahmen.
Aufgaben und Anforderungen zur Lösung
Die aus der Analyse resultierenden Maßnahmen werden in Änderungsanforderungen oder Aufgaben umgesetzt, die das Problem lösen. Beides kann direkt im Detail des Fehlerfalls oder im Detail der Eigenschaft erstellt werden. Die Anforderung oder Aufgabe wird mit dem möglichen Fehler verknüpft. Dadurch wird ersichtlich, warum die Anforderung oder Aufgabe entstanden ist, und es kann verfolgt werden, ob sie gelöst wurde.